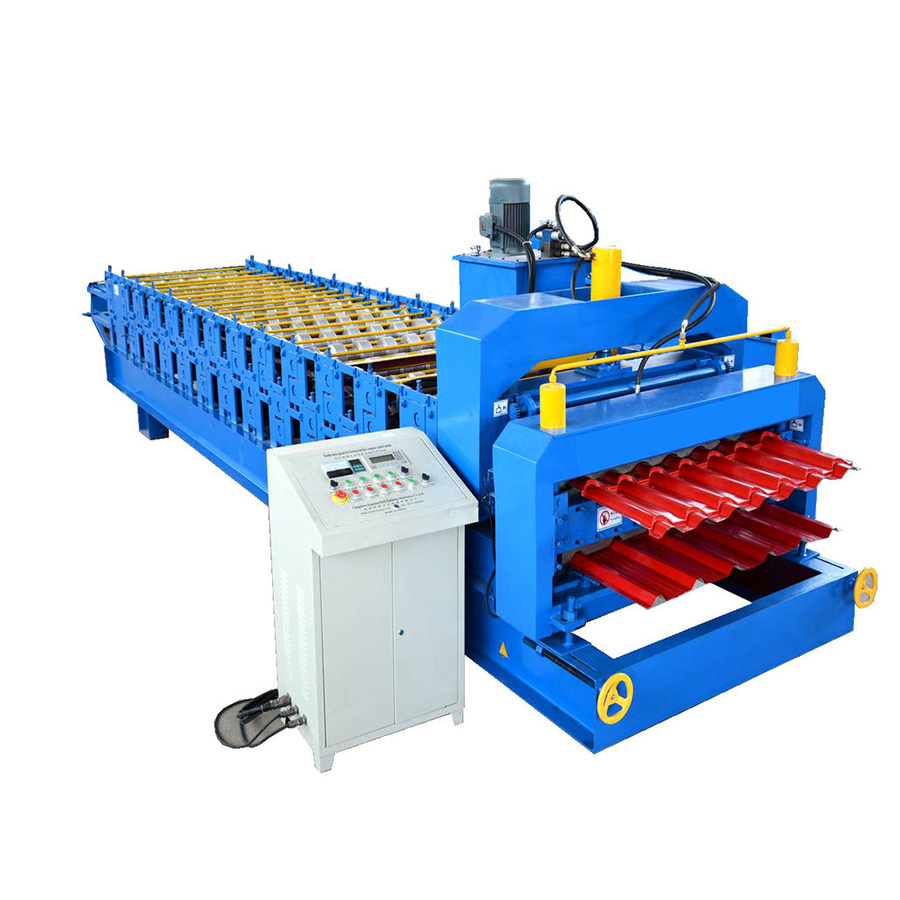
Automatic Double layer roll forming machine
layer double machine roll forming cold roll forming
double layer roof sheet roll forming machine
steel double layer roll forming machine
hx-color steel double layer roll forming machine
double forming layer machine roll
layer double machine roll forming
double layer roll forming machine willingint
double-layer roll forming machine
double layer glazed roll forming machine
double layer roll forming machine price
double layer roll forming machine roofing sheet
double layer roof roll forming machine
Machine Quick Details | |
Model Application: floor deck and roofing | Condition: New |
Type: Roll Forming Machine | Brand Name: Frametec |
Applicable Materials: PPGI | Forming Speed: 20-25m/min |
Warranty: 1 year | Place of Origin: China |
Features of the machine:
Our Automatic Double layer roll forming machine consists of decoiler, feeding and levelling device, pre-shear, roll forming system, hydraulic post cutting, run out table, hydraulic station and PLC(controlling system).
Long production line, good profile shape on final products; Time saving and labor saving, which is highly improved production efficiency and suitable for current production. This machine is easy to operate and run stable with good precision.
Flow chart: De-coiler – Leveling device -- roll forming parts -Post Cutting system– Stack
PROFILE
MATERIAL:
1 ) Effective Coil Width: 1010/900mm
2 ) Suitable Coil Thickness: 0.4-0.5mm
3 ) Suitable Raw Materials: color steel sheet
4) Yield strength of raw material: 245Mpa
Main Components:
1. Hydraulic decoiler with coiler car
Features: Mandrel and basement are the two components of the decoiler, the mandrel is shrinking expanding by mechanical device manually, after fix coil to mandrel, then put back the coil with mandrel together to basement.
Power: None;
Power of the open and closure of segments: Mechanical;
Power of rotation of segment: Pull by forming system;
Number of segment: 4pcs;
Range of segment expansion: 460 ~ 520mm;
Height of center of the mandrel: 0.65m;
Feeding speed: depend on the roll forming machine speed;
2.Sheet guiding device
Features: Ensure smooth& precise material feed.
Components: steel plate platform, two pitching rollers, position stopping block.
The coil is guided in the correct position and passed to the roll forming equipment
3.Roll-Forming M/C:
The main frame of machine is welded separately and the outside wall is connected by screw after being rot blasted on the surface.
Roller Material is high grade No.45 forged steel, with digital-controlled procession.
Shafts of rollers are tooled by grinding machine for two times to ensure the precision of final product.
The rollers are plated with hard chrome with thickness of 0.05mm on the surface after being machined by the exact machine tool. So that ensures long life of forming rollers.
4.Hydraulic Post Cutting
Function: cutting action is controlled by PLC. The main machine automatically stops and the cutting will take place. After the cutting, the main machine will automatically start.
Power supply: hydraulic station;
Frame: welding steel frame;
Stroke switch: non-contact photoelectric switch;
Cutting after forming: cut the sheet after roll forming to required length;
Length measuring: automatic length measuring
5. Hydraulic station:
It is controlled by gear wheel oil pump. After filling the hydraulic oil into the hydraulic oil tank, the pump drive the cutter machine to begin the cutting job.
Match equipment: The system includes a set of hydraulic tank , a set of hydraulic oil pump, two hydraulic pipes.and two sets of electromagnetism valves.
Adopted top brand hydraulic system components to ensure the stability and lifetime, avoid leakage.
Supplies the initial power to the cuter through a closed oil tank. It is off without cutting, which can save the power.
6. Profile Stack
Un-power, total 3 units, with roller on top stack for easy movement
Profile effects:
Customer Inspection
Our Factory
Why Choose us:
13 years’ manufacturing experience in high quality equipment for cold formed steel structures.
Competitive price and good quality
One year free warranty
Fast response of after sale service
Can be customized by clients’ requirements
Easy operate and easy to maintain
Self-developed of post cutter, one blade to cutter all size of final products